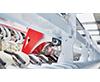
Automation 4.0 with Bobbin Cloud, the revolution in material flow
With the Bobbin Cloud material flow system based on the latest RFID technology, the Autoconer X6 guarantees maximum process reliability thanks to clever, software-controlled material management. RFID chips turn Pegtrays into intelligent SmartTrays. They are the key to high-performance bobbin and tube logistics with comprehensive material tracking; the status and position of all SmartTrays are known at all times.
Characteristic features of the Bobbin Cloud are the decentralised processing aggregates and the ingenious material flow designed in a round loop. Like during a pit stop in Formula 1, the bobbins and tubes automatically move to the processing aggregates positioned along the movement paths. To increase cycle speed and capacity, several bobbin preparation stations can be installed which operate in parallel. The winding units are reliably supplied with prepared bobbins directly from the Bobbin Cloud. The entire circuit functions as a material storage area; RFID ensures intelligent distribution and a targeted assignment of the SmartTrays with bobbins, residual bobbins and tubes.
The new optical tube inspector with infrared sensor is another important part for increased process reliability. With noncontact scanning it reliably detects single yarns and all yarn structures even at high cycle rates.
Bobbin Cloud and RFID technology are the basis for a future-oriented direct link between Autoconer and ring spinning machine, with integrated online quality monitoring system SPID. This means every spinning mill now has the opportunity to establish its quality level at the highest standard. Optimum machine networking and more intensive process automation are becoming the standard.
Energy: up to 20% reduced resource consumption
A comparison of the performance of the 5th and 6th Autoconer machine generations not only pays off in terms of process automation. The Autoconer X6 also offers attractive energy consumption reductions of up to 20%, which is mainly due to its high energy efficiency. All components and functions have been optimised in terms of energy. These measures include improved aerodynamics in the airflow, state-of-the-art drives with high efficiency levels and the unique "Power on Demand" vacuum control.
Further energy savings have been achieved when it comes to keeping the machine clean. MultiJet enables compressed air consumption to be drastically reduced, the bobbin dust removal system requires significantly less energy thanks to new aerodynamics, while the travelling cleaner is characterised by higher energy efficiency.
With continuous online monitoring of compressed air and energy consumption, Energy Monitoring helps the operating personnel to optimise winding processes in an energy-efficient manner and thus reduce costs.
But above all, the Autoconer X6 conserves the most valuable resource, the yarn, through perfectly coordinated winding and cycling processes. Here, Schlafhorst achieves unique improvements with a comprehensive complete solution. The upper yarn sensor, aerodynamically optimised suction nozzle, SmartCycle with intelligent cycling sequence and SmartJet in the doffer work in perfect harmony.
Economics: up to 6% higher productivity
The Autoconer X6 is consistently designed for maximum economy. This begins with the setup and commissioning of a new production line, which can be carried out much faster with the new generation of machines. The functional design of the sections with integrated superstructure allows preassembly and preadjustment even before they leave the factory, so that valuable time is saved on site during installation and setup in the spinning mill.
Extra-long machines with up to 96 winding units increase productivity per square metre. The Bobbin Cloud reliably supplies all winding units along the entire length with material at the highest cycle rates. With the Autoconer type RM, the unique 9+1 feed principle proves its worth in the extra-long machines.
The intelligent winding technology of the Autoconer X6 is the secret of its extraordinary production performance. LaunchControl accelerates the Autoconer X6 without slip to the desired maximum speed. Eco-Drum-Drive, high-speed anti-patterning and the TensionControl and Autotense FX yarn tension systems ensure high-speed quality without compromises. Productive cycling processes that are as short as possible with SmartCycle and SmartJet as well as numerous autocalibration functions optimise the winding process in many places and ensure measurably higher productivity.
Ergonomics: intelligent reduction in personnel workload
The issue of personnel availability – in terms of quality and quantity – is already today an important factor in the textile industry and will become even more important in the future. With its smart and clever functions, the Autoconer X6 reduces the general personnel requirements in the winding department on the one hand, and noticeably relieves the workload on employees thanks to intelligent operating comfort on the other. The smart X-Change doffer ensures intelligent package handling thanks to SmartJet, Tube Check, multi-tube handling and empty tube strategy. The new intermediate storage doubles the storage capacity of the finished packages, allowing production, doffing and personnel capacities to be optimally coordinated.
Via the Informator, the production of every single quality package is monitored. Modern sensor technology and the autocalibration of many aggregates make Schlafhorst's textile technology knowledge available at the push of a button. This ensures maximum machine performance and relieves the pressure on the personnel situation in the winding department.
Benefit from the quality benchmark
Autoconer packages are considered to be the benchmark for package quality in the textile industry – both in commodity and special applications. Even in its basic configuration, the Autoconer ensures high-quality packages with many functional details; their package build offers high process reliability and thus higher benefits in downstream processing. With innovations in splicing technology, the Autoconer X6 offers interesting possibilities for successfully processing modern, sophisticated yarns. Using Autotense FX, Variotense FX, Propack FX, Variopack FX, Ecopack FX or PreciFX digital laying technology, spinning mills produce higher-quality packages in an optimised process which stand out with their unique properties in further processing and redefine cost-effectiveness in the high-end sector.
The Autoconer X6 shows the textile industry the way to a more profitable future: with its E³ certification for triple added value in the areas of energy, economics and ergonomics. Groundbreaking steps are being taken in the direction of Automation 4.0 with data and process networking, especially in the new and revolutionary Autoconer material flow system called Bobbin Cloud.