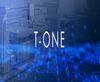
What will be the next step forward for nonwoven production? Revolutionary web forming or web bonding processes? A fantastic new machine? Or a sustainable raw material that is cost effective and easily processable for mass production?
No. Digitalization is going to take nonwoven production to the next level by massively reducing conversion costs. And it’s already happening…
T-ONE is a digital working environment that supports all production employees with their daily work – from plant operators and quality control staff through to process supervisors, product engineers and the management team. It is programmed as a client-server program, with a database installed on a server that the customer controls. It can be used on Windows-based computers.
Addressing Common Efficiency Problems
T-ONE tackles the biggest challenges for efficiency and product quality in production, and offers exciting potential to significantly boost performance.
Here are three specific examples:
Efficiency Problem 1: No central base to store data about products and production. Spending time searching for documents or information brings efficiency down. If there is no central place to store data, everybody creates their own data set. As a result, multiple versions of the same data exist and it takes longer to search for the up-to-date version. Errors and mistakes can also happen when working with an outdated version. A central database with a clear timeline eliminates these problems.
Efficiency Problem 2: Data-driven tasks that can be digitalized – but are not (yet!) Performing the same task manually again and again frustrates employees and leads to errors. Recipes are a strong example: If a recipe with more than two hundred proven line settings is not digitally transferred to machines, errors can occur when typing in the values manually.
Efficiency Problem 3: Inexperienced or insufficiently trained staff. New employees tend to work more slowly – and make more errors. Digital guidance can help to ensure quality and efficiency. In addition, new workers react less quickly and less effectively than experienced operators when production line performance or product quality deteriorates, or when something unexpected happens. Software can suggest optimal line settings to reduce waste and support consistent performance.
Functions for better operations
When it is fully implemented, T-ONE provides benefits including:
-Collecting relevant production-related data in one place, and providing access to current and historical data.
-Implementing best practice and routine work processes.
-Helping to analyze inefficiencies and implementing a continuous improvement process.
-Visualizing current and historic product and process quality.
-Simulating line behavior before line settings are changed in the machine.
-Suggesting new line settings for optimized process efficiency.
The functions described above are implemented via several modules (see figure below). Each module supports a specific task, and adds or uses data from the central database. The Quality Management module, for example, manages customers’ product specifications and a roll’s quality data. It describes routines for testing every parameter required by the specification, and creates any necessary certificates. The module also collects testing values from laboratory instruments, stores them in the central database, and visualizes them for every roll produced.
Easy Integration into Your Production Environment
T-ONE is not one great big block. Users can choose between basic and extended packages, so the specific investment depends on the unique machines in your line and your preferred choice of T-ONE modules. The standard implementation procedure involves consulting, customization, installation and training. Experience with installations show that the investment pays off in less than one year.
To maximize the positive impact of T-ONE, the software should be customized to your individual requirements and IT environment. T-ONE is an open software package, so interfaces with existing solutions can be programmed if the software allows it. This has already been done in relation to existing SCADA-based programs, and even with Enterprise Resource Planning (ERP) systems.
T-ONE in a Nutshell
T-ONE is a complete digital environment built around a central database. It supports quality control, recipe management, process documentation, KPI/continuous improvement and process optimization. When a new function is required, it can be added as a new module – just like the Energy Management System in mid-2022. T-ONE can be customized to address your exact requirements and to fit into your existing IT landscape seamlessly. These features make T-ONE an essential tool to support your journey to operational excellence.