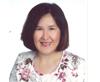
Innovations and Trends for Combed Cotton
Although ring spinning has always been strong in west hemisphere, the combed cotton yarn production has considerably decreased. It is known that many companies started to invest in order to make use of the demand generated by this. The energy consumption of the combing process has been reduced by 48% thanks to the innovations. In addition, the importance to adapt to changing market conditions and raw material quickly is getting more important day by day.
The TCO 12 combing machine developed by two leading textile companies, Toyota and Trützschler, manufactures repeatable, continuous high quality combed cotton slivers with a 600 carding/min speed. The contribution of Toyota Company in developing this this machine is reducing the vibration created by the conventional gear drive system, which has already reached limits, with the special servo engine technology (2-twin-drive). Individual motors to synchronously drive the combing elements on both sides are used. This minimizes the torsion of the elements and the vibration of the machine by 25% and the combing machine’s vibration by 25%. Through the DISC MONITOR system used by Trützschler company on its Draw Frames, the sliver number is continously followed.
The innovation of the E 80 combing machine introduced at ITMA Asia + CITME 2012 is 45 % greater combing area, which enables the focus, freely selected by the customer, to be concentrated on productivity, quality or raw material yield by using a 130° round card. This has led to an improvement of 20% (IPI) in the yarn quality. It has been stated that the carding speed increased up to 500 carding/ min and the production performance increased by 80 kg/ h. Combed sliver production of up to 2 tons daily and use of 1.000 mm cans is achieved with
E 80 comber with fully automated lap change and ROBOlap piecing system.
The LK64Z using the MCD PLUS technology offered by Lakshmi Machine Works (LMW) for the combing chamber has a daily production of 17 tons and a production speed of 500 carding/min. LK69 combing machine offers a production of 600 carding/min and 2,1 ton/daily thanks to a technology named PACT. The combing machine can be configured in order to meet the needs of the next process. For instance: with two supplementary cans of 24” and an automatic cans shifter for the exit (exit of 40" – on request with a supplementary can). Other advantages are the elimination of short staples, improved doubling and attraction, and it can shorten the installation period by providing the combing machine in two modular structures.
Innovations and Trends for Rowing Frames and Ring machines
The spindle numbers of machines are increasing. The reason behind this is to reduce the fixed costs remaining within the kilogram yarn production cost and to increase the economic efficiency. By enabling energy savings, it is important to consider to reducing the maintenance and processing costs during the machinery design. The effect of this has been reflected to all ring machines manufactured by all machinery builders.
The LF 4200 Flyer offered by LMW is the longest Flyer with its spindles up to 200. The LR 9 model ring spinning machine using 4 -Quadrant motor drive for T-Flex driven system offered by LMW has up to 1.824 spindles. Toyota RX300 operating with high efficiency and energy savings thanks to the use of “The new super energy saving motor” and the special invertor technologies has 1.824 spindles. Zinser 351 using SynchroDraft double drive system for super long machines has 1.680 spindles. The Rieter ring spinning machine having FLEXIdraft, ROBOload features and designed as G35 modular has 1.632 spindles.
The spinning triangle is narrowed by intensifying fibers with different systems on compact spinning machines. Here, companies try to improve these designs protected with patents. Rieter’s K 45 model compact ring machine’s system having 1.632 spindles is the intensifying of the fibers with perforated metal cylinder. Thus the costs of energy and maintenance can be said to be reduced.
When dirt particles carried by fiber mass reach the compact unit at the Zinser 351 Impact FX compact ring spinning machine, they are removed by being absorbed through the perforated apron by compact air absorption. This model is the longest compact spinning machine with 1,680 spindles.
LMW’s LRJ 9 compact ring spinning machine has up to 1.632 spindles using perforated synthetic apron.
Innovations and Trends for Open-End and Air-Jet Spinning Systems
The Rieter Company has considerably reduced the energy consumption thanks to the use of energy saver motors and economic invertors’ cooling systems besides the R 60 using an efficient vacuum system and a smart cleaning system. It is the longest open-end machine in this field with 540 rotors and it provides ease of use thanks to its easily changeable parts.
The Autocoro8 rotor spinning machines developed by Oerlikon-Schafhorst and spinning yarn at 200.000 rpm rotor speed has 480 spinning units, each of it having an electromagnetic drive. The better digital controlled bonding technology DigiPiecing and winding with DigiWinding, the best bobbin for the next process enables efficiency and productivity.
The air jet spinning machine J 20 has a high performance and flexibility as it can process two different materials in both sides. Rieter informs that 30/1 NE yarn from 52% PES-48% combed cotton is manufactured at a 400 m/min speed. This signifies the capacity of J 20 to manufacture yarns from diversified blends.
As a result, the increases in the raw materials cost direct options to blends in the textile industry. Viscose and polyester in the mixtures are still keeping their places in cotton blends. Without ignoring the possibility of textile industrialists to use different fibers, we are at a period, in which we need to configure the machinery selection for flexible working. As always, the energy costs will be high in our country due to the energy dependence to overseas. Besides all these, technologies constantly developing in nano technology, electronic and software necessitate to re-define our work. That’s how a dynamic Turkish Textile Industry will adopt itself to this situation.