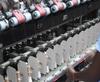
Uster, Switzerland, 10th December 2019: Even in the best ring spinning mills, there is always room for improvements, among a complex range of options management and operatives need to consider for optimized productivity and profit. USTER® SENTINEL provides a fact-based overview of spinning machine performance, pinpointing real opportunities for excellence in the use of technology, components and manpower.
“The biggest challenge in my job is to source skilled shop floor operatives and retain them in the long run,” says M. Kannan, General Manager responsible for technical and factory administration at Kikani Exports. The mill – obviously a well-run unit – is located at Dholka in the Indian state of Gujarat. It runs with an installed capacity of 29,376 ring spinning spindles and 4,320 twisting machine spindles. To improve the manpower situation, the mill prioritizes progressive HR policies and a decent working environment, as well as investing in sophisticated production machinery.
Wide-ranging benefits in ring spinning
“We invested in USTER® SENTINEL ring spinning optimization system with the goal to improve profits but we are delighted that staff also likes the installations,” says Vrajesh Kikani, Managing Director, Kikani Exports. The mill reports a positive impact on profitability resulting from successful optimization of a number of factors, such as waste, ring traveler lifetime, machine speed and energy consumption etc.
Production focuses on 100% cotton combed compact yarns, in the count range Ne 20 to Ne 40, for weaving and knitting end-uses. The mill has been able to reduce waste by half since installing USTER® SENTINEL. Enhanced overall productivity is a consequence of reducing pneumafil waste. USTER® SENTINEL also monitors the productivity of all spindles, feeding back all the required links and information to help yarn producers make optimization decisions at ring spinning based on reliable data.
Among potential problems for all spinners is inconsistent yarn quality characterized by low twist, caused by loose fibers blocking travelers – especially excessively worn ones. Only USTER® SENTINEL can identify spindles malfunctioning in this way, since the issue does not cause end-breaks but still produces yarns which are too weak for high-speed warping and weaving machines. Then unique Off-Standard feature of USTER® SENTINEL safeguards against ‘hidden’ quality risks such as this.
Bobbin build-up report gives practical support
End-break levels are a key indicator of ring spinning performance, and USTER® SENTINEL recognizes this by providing an intuitive bobbin build-up report for every parameter influencing end-breaks. Spinners can then initiate improvements relative to their own mill, taking account of ambient conditions and energy consumption, as well as machine speed, wear of mechanical parts and personnel.
The bobbin build-up report also provides for higher performance, along with optimized cops. Comprehensive analysis of the speed curve – and its impact on quality throughout cop build-up – is a key element of the enhanced way of optimizing ring spinning performance. Cop build-up quality is the new dimension of optimization, enabling managers to select the correct machine settings for higher production yields, while keeping quality at the desired levels. Furthermore, it is now possible to compare ring spinning performance between different machines.
“The bobbin-build up report offers us potential savings on travelers, optimizing their lifetime,” says Kannan. He makes use of this facility for ring traveler performance comparisons by using the end-break information to indicate the end of traveler life cycles. The bobbin built-up report allows the mill to monitor traveler wear related to age, checking stable end-break rates through the entire doff duration. This report shows the current state in intervals of five minutes, and an overview provides information about end-breaks per 1,000 spindle-hours.
Fact-based feel-good advantages
Reports give status information at five-minute intervals, including end-breaks and piecings during that period. “Information about piecing speeds helps me to identify each operator’s skill level so that I can optimize the operation schedules and processes. Only by assigning manpower carefully it is possible to maintain ideal working conditions,” says Kannan. USTER® SENTINEL handles complete personnel management, including shift planning and staff assignment for all machines in the system – integrated with monitoring of critical ring spinning parameters. This makes personnel management in ring spinning fact-based and less time-consuming.
Reliable detection of slip, rogue and idle spindles is what makes USTER® SENTINEL popular among shop floor staff. LEDs indicate spindles showing an issue or positions where an end-break occurs, directing personnel quickly to fix the problem. Incidents are also shown on the machine display, providing an overview of spindles where attention is needed. “Operators really enjoy working thanks to USTER® SENTINEL, as it makes it easy to spot an end-break, even when patrolling far away. They enjoy the experience of handling their job efficiently and are under less stress – both of which increase the feel-good factor at work,” says Kannan.
The long view
Optimizing the potential of ring spinning covers many aspects, taking advantage of USTER® SENTINEL and the data it provides: waste saving, compressed air saving, energy saving, cuts saved at winders and increased productivity and quality. Says Kikani: “USTER® SENTINEL works as a ring spinning optimization system, increasing profitability where it matters most…every day.”
Kikani visited the USTER booth at ITMA 2019 in Barcelona. He was interested to learn about further technologies and how a mill will be managed in future. “I’m amazed about the advantages for ring spinning through connectivity. I can see more profit optimization potential. With USTER® SENTINEL and USTER® QUANTUM already installed, only USTER® QUALITY EXPERT is needed to correlate ring quality data and winding quality data in a single system.”
There is one key performance indicator still not integrated the system but no less important to the company: “Enjoyment. A happy staff supports great performance and is a positive cost factor for the mill in the long run,” says Kannan.