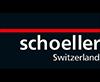
The 150th anniversary of Schoeller is an indication of the many innovations the company has brought to the textile sector for years. The company launched its first elastic ski suits in the early 1960s, after Kevlar's integration into motorcycle jackets in the early 1980s, it produced the first heat setting fabrics twenty years ago.
In the village of Sevelen, near the Austrian border, the Schoeller company, a natural extension of the Swiss Alps, is now the winner of many award-winning and exclusive fabrics. Most of these products are licensed for third party manufacturers. Coldblack® for UV protection; energear ™ to keep infrared away from the body; NanoSphere® for useful properties for water, oil and dirt retention, and for high wash and abrasion resistance for moisture management; 3XDRY® for humidity control, and the newest environmentally sensitive Schoeller technologies, ecorepel® and ecodry are just some of them. Preserving its leadership in the field of stretch-woven fabrics for many years, Schoeller is expanding its range of fabrics in 2012 with the acquisition of the Swiss manufacturer Eschler Group.
Worldwide Standards
Production in Switzerland, of course, comes with environmental responsibility - the country ranks number one in the Environmental Performance Index (EPI) worldwide and as a result of this achievement, Schoeller has reached higher standards than other European companies. In this context, in 2001, Schoeller became the world's first textile company to receive bluesign® certification.
Minimal Application
Michael Killisperger from the Schoeller finishing and coating department explains the whole application process as following; “It is not possible to finish the layers one by one before hot melt lamination, so that the fabrics and membrane films are painted separately before laminating and then assembled by the Eco Applicator before going to the stent. The Eco Applicator is designed for minimum application and we can measure the humidity at the inlet of the unit and then go through both the first and the second pass.”
The company is part of the program that invests in new technology at the Schoeller plant over the last decade, and has introduced new product developments, such as the introduction of Uppolicated Econyl® yarns (Aquafil SpA). Ecorepel® Bio technology without PFC, based on renewable raw materials, has provided new components for the company's industry-leading membranes.