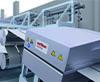
World premiere at the international Itma trade fair in Milan: for the first time, Oerlikon presented its innovative new development, the EvoSteam, for manufacturing PET staple fibers. Visitors to the Oerlikon trade fair stand were extremely interested in the new, innovative technology, with business discussions very clearly showing that the new development fulfills the needs of potential clients. The EvoSteam process convinces both in terms of its energy, water and raw material savings and also with regards to lowering operating expenses and the carbon footprint – simultaneously with excellent fiber qualities.
Visitors to the trade fair spoke about a pioneer for more sustainable staple fiber production. “This shows that our customers have understood that the EvoSteam process has tremendous potential and represents a huge step forward” comments Martin Rademacher, Head of Sales Oerlikon Neumag, thrilled by the across-the-board positive trade fair feedback in Milan.
Performance in Numbers
When developing the EvoSteam process, our engineers focused both on fiber quality and in particular also on sustainability, energy efficiency and reducing the consumption of resources. Compared to conventional staple fiber systems, an increase in efficiency of up to 12%, a reduction in production waste of up to 50% along with energy savings of up to 8% speak a very clear language. With water savings of up to 10 million liters per annum and a lowering of the carbon footprint by up to 20%, this Oerlikon system helps fiber manufacturers achieve their sustainability targets.
EvoSteam Process dispenses with Liquid Baths
10 million liters less water: the function of the immersion bath is assumed by a carefully-coordinated setup comprising godets and pulsed spray nozzles. Consequently, moisture is precision-metered and added to the process as required. Completely dispensing with liquid baths generates significant savings in terms of water, energy and spin finish, while simultaneously also increasing occupational safety and cleanliness at the production line. “In conventional drawing processes, large volumes of water are used to control the temperature and provide the requisite moisture in the fiber tow. At the end of the process, this water must be removed from the tow again, which is a very resource- and energy-intensive process” states Martin Rademacher. “The sparing utilization of water enables a significant reduction in the requisite drying energy, which translates into a tremendous cost benefit for our customers.”
Optimized draw Point Release and Improved Drive Concept
Up to 12% superior efficiency: the new, optimized draw point release permits higher production speeds and hence increased production volumes. The fiber draw point is released by a precisely-focused vapor curtain, is now carried out more evenly and dramatically minimizes the friction between the filaments in the tow. In addition, an innovative drive concept reduces yarn slippage on the godets, improves the process stability and hence increases system availability. Both technological innovations improve the yarn quality demanded by the downstream processes and which play a decisive role for manufacturers’ margins.
Spotlight on Reducing Waste
The development focused not only on resource-efficient fiber production and improving the fiber qualities, it has also been designed to dramatically reduce the waste generated when manufacturing with this system concept. Martin Rademacher comments on this: “With all the optimizations, we promise a 50% reduction in production waste.”
About Oerlikon Polymer Processing Solutions Division
Oerlikon is a leading provider of comprehensive polymer processing plant solutions and high-precision flow control component equipment. The division provides polycondensation and extrusion lines, manmade fiber filament spinning solutions, texturing machines, BCF and staple fiber lines as well as nonwoven production systems. It also develops and produces advanced and innovative hot runner systems and multi-cavity solutions for the injection molding industry. Its hot runner solutions serve business sectors, including automotive, logistics, environmental, industrial applications, consumer goods, beauty and personal care and medical. Moreover, Oerlikon offers customized gear metering pumps for the textile, automotive, chemical, dyes and lacquers industries. Its engineering competence leads to sustainable and energy-efficient solutions for the entire polymer processing value chain with a circular economy approach.
Oerlikon Polymer Processing Solutions Division serves customers through its technology brands – Oerlikon Barmag, Oerlikon Neumag, Oerlikon Nonwoven and Oerlikon HRSflow – in around 120 countries with production, sales, distribution and service organizations.
The division is part of the publicly listed Oerlikon Group, headquartered in Switzerland, which has more than 13 000 employees and generated sales of CHF 2.9 billion in 2022.